Flat Honing and Lapping with Two-Wheel Machines
The Basic Lapping / Flathoning Process
As described in the reprint “Die Lapp-Technik” (The Lapping Technique”), the removal process involves hard grain rolling on the workpiece, which then moves in turn.
Figure 3: Procedure with Loose grain Figure 4: Removal Procedure
Magnification approx. 3,500 times
Figure 5: Procedure with bound grain Figure 6: Honed surface of workpiece
Work-piece surface honed with cutting grain material St 50, surface roughness Rt=0.5 microns, 1,350 times magnification
The procedure shown in Figures 3 + 4 requires a single-wheel lapping machine, as shown in figure 7, where dressing rings are used for holding the workpiece and correcting wear. The work-piece holders or jigs are being in position loosely in the dressing ring. The working wheel is dressed continuously during processing. As a result, a correction coefficient of over 100% can achieve by adjusting the dressing rings, which means it is theoretically impossible for a flatness error to occur.
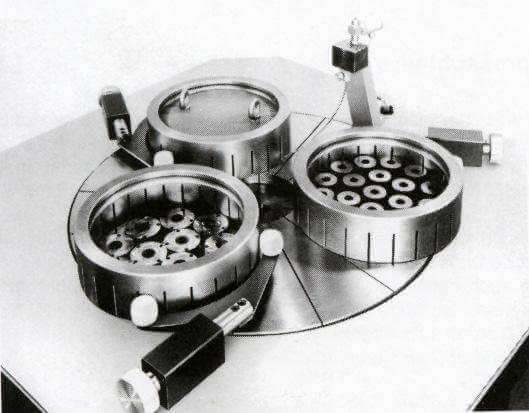
View of a simple lapping machine
From figure 8, it is clear that the workpieces of the two-wheel machines must be held in the carriers or also known as jigs. There is a force to rotate clockwise that’s driven by a pin ring or toothed ring. In this way, the workpieces are drawn across the entire wheel surface. The upper working wheel is moved up a counter-pressure and the removal is carried out by the constant reapplication of the grain in between (figures 3 & 4). The upper and lower working wheels drive individually and their speed and direction of rotation are being modified at will. Figures 5 & 6 show the “Flathoning” procedure, cf. Chapter 6.
In contrast to Figure 7, we now turn the two-wheel principle, which cannot use any dressing rings in the working process. The wear is only corrected by the arrangement of the workpieces, the shape, and size of the workpieces, the exposure, and the change of the rotation direction.
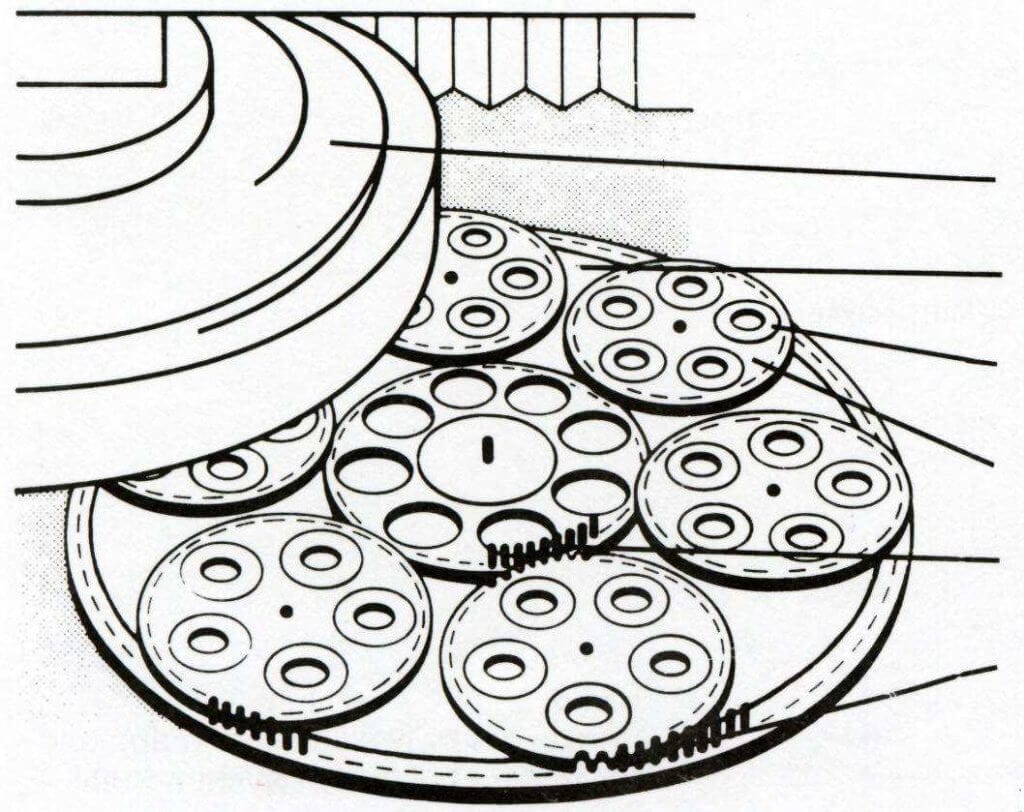
1.Upper working wheel
2. Lower working wheel
3. Workpiece
4. Work holding plate (workpiece receiver)
5. Inner pin or toothed ring
6. Outer pin or toothed ring
Figure 8: Two-wheel definitions
The exposure is determined and/or restricted by the type of workpieces. The wear coefficient of the working wheels can be influenced strongly by the arrangement and number of the workpieces. It will never be possible for the correction coefficient to reach 100%. It is occasionally necessary to interrupt production for additional dressing or cutting. An additional description of these important functions can be found in Chapter 8.
Characteristic properties of flathoning with planetary kinematics
Machine Set-up
- Tension-free mounting of work pieces in a receiver cutout
- Self-correction through oscillating suspension of upper working wheel
- Force-linked feed, volume of time savings not strictly specified
- Attractively priced devices for various work pieces
- Short conversion times
- Restricted to homogeneous functional surfaces (flat, concave, convex)
- Variable processing of components in batches
Process technology
- Even load over the entire functional surface due to laminar application
- Direction of action parallel to work-piece surface
- Comparatively low cutting speeds and grinding pressures and grove damage
- In-homogeneous load on grinding wheels
- Cyclical change to the processing conditions due to planetary kinematics
- Undefined micro-kinematics in auto-rotation of the work pieces
Work result
- Undefined curved, superimposed machining tracks (similar to cross grinding)
- Excellent surface qualities and shape accuracy
- improvement in the shape accuracy compared to the original status
- Reduction in the divergence of thickness in the work pieces
- Possibility to align functional and cladding surfaces for cylindrical work pieces
- Fluctuating distribution of the grinding allowance on upper and lower sides of the work pieces
- High removal volume/time
- High G values