Flat Honing and Lapping with Two-Wheel Machines
Description of a Two-Wheel Machine
From a distance, a two-wheel may appear to be a simple machine without any real complexity. It has two rotating working wheels with some lapping compound between them and a rotating pin ring. However, that is only true to a certain extent! The decisive factors are not only the mechanics but also the know-how based on decades of experience.
Let’s start by looking at the flat honing machine set-up
One principle, we should differentiate between the design of lapping and flat honing machines. Excellent stability and extremely precise bearings are of crucial importance, as is the sensitive operation of the working wheels controlled by state-of-the-art technology. The lower section of the housing accommodates the bearing of the lower working wheel plus the inner and outer pin or toothed ring. The latter must be well protected against soiling, especially as the lapping compound and/or the removal are fatal for mechanical bearings. There is generally a closed-circuit cooling system for the working wheels. The coolant flows through up to three rotation axes, which seal suitability.
The carriers are each driven internally or externally by a pin ring or a toothed ring. These pins absorb considerable forces and it must also be possible to lower the outer one for attachment of additional devices (cf. Loading and unloading fixtures, Chapter 10).
It should be easy to clean the entire working area. Good dirt drainage, a ring flush and a shower are necessary.
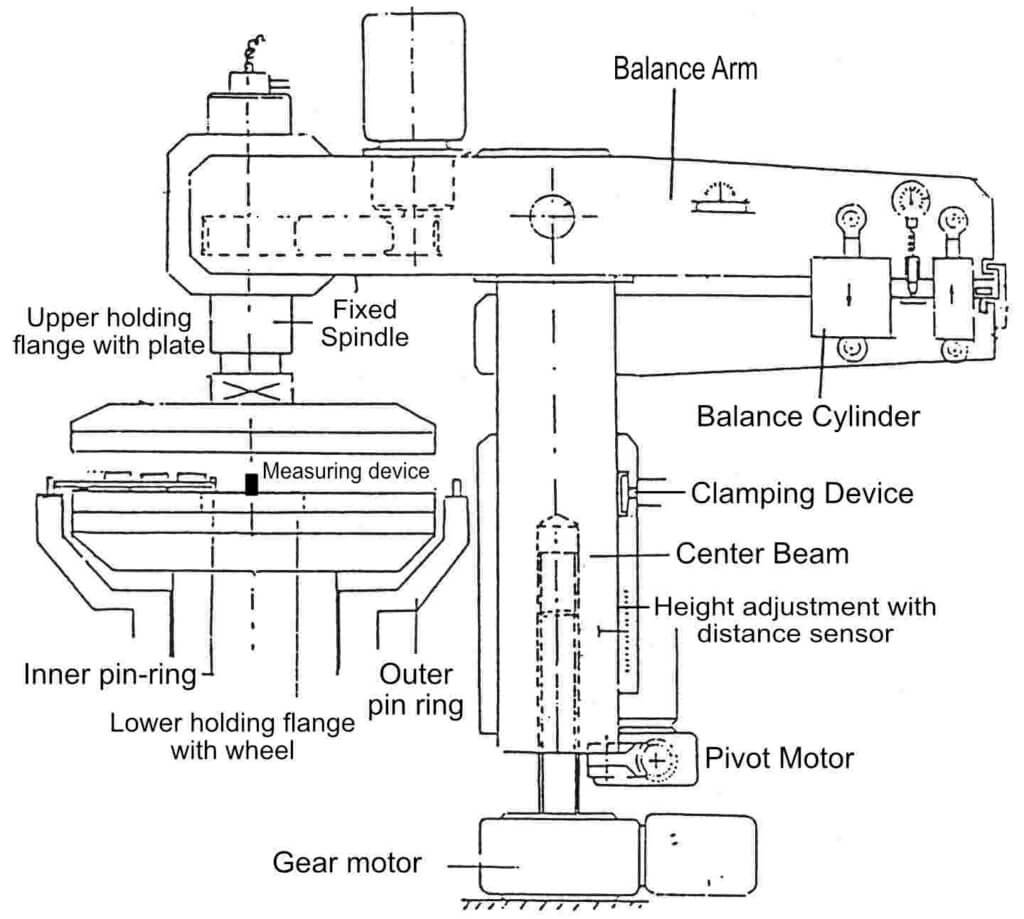
Principle of a two-wheel lapping machine
Severe demands are placed on the drive of the upper working wheel. A stable suspension and/or bearing is an essential prerequisite, for the torque receiver and the load control as well.
What are other factors?
Mastering the load in connection with mechanics that are as reliable as possible, electronics and modern controls/algorithms is probably the most important, but also the most expensive are of the machine. In most cases, the heart of the machine is found in the types of bearing, suspensions, and in-feed. In terms of the requirements, the upper working wheel must be as fast as possible and yet also position itself very gently on the workpieces. Firstly, its own weight must be compensated. Then it must be possible to regulate the load extremely precisely and with infinite variations. Theoretically from zero up to the highest end value. Because of the osculating suspension of the upper working wheel, the coolant supply and/or return line must not be rigid, even if the upper section has a pivot away laterally and/or radially.
Production with controlled measurements demands the integration of measurement devices into the machine (in-process measurement). A central probe, fed through the upper spindle, is a possible variant. Direct measurements from the outside are generally more complicated and more expensive. (Figure 34)
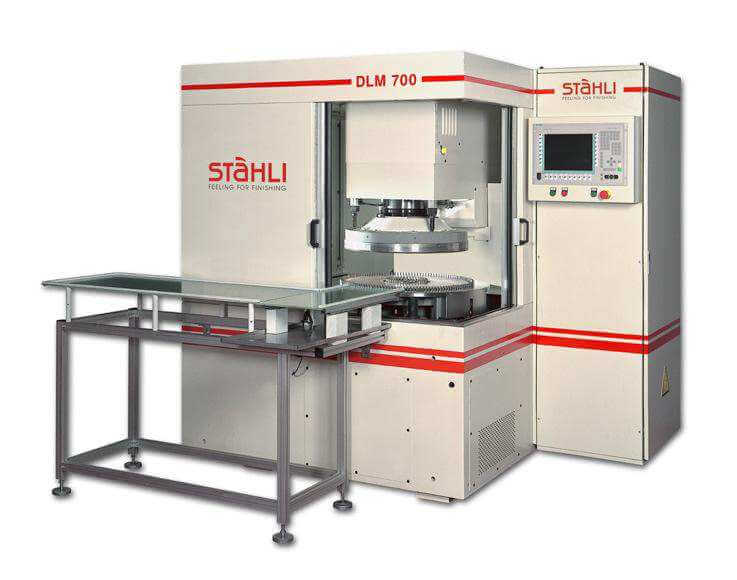
Flathoning machines evolved from lapping machines
The following issues have to be mastered
- The High dead weight of the working wheel and/or the machine head (mass inertia)
- A possible angle error between the upper and lower working wheels due to the various loads and manufacturer tolerances
- The sensitive vertical adjustment of the upper drive. The spindle with its own friction in the seals, designated as “slapstick” or adhesion
- The torque building of the drive spindle must be up from the outside via a spline shaft, a belt or direct drives. This generates considerable frictional resistance on the axial offset (in-feed).