The Technique of Lapping
Lapping
Even back in the Stone Age, lapping was used as a means of fashioning tools and implements. By rotating a stick against a surface strewn with sand, our early ancestors managed to drill holes: Undoubtedly the first “machining” process ever invented. A drawing from the German Museum in Munich (Figure 1), which was produced on the basis of archaeological findings and research, shows how one of these primitive “lapping machines” might have looked.
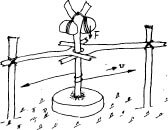
The drawing shows exactly the principle corresponding to the lapping process. The use of rotational friction, speed, load and the addition of sand grains and fluid result in lapping or drilling. The drawing also shows that -consciously or unconsciously – several factors already influenced the result of material removal. The material of the tool (drill), the grain (hardness and shape), the tool speed (rubbing or cutting speed), the added fluid (e.g. water) and the variable load of the tool or workpiece (surface pressure) all influenced the result.
Wood was, of course, an ideal material for carrying the sand or lapping particles, and the worker could obtain different results by choosing sand of various types and hardnesses. The work progressed more or less rapidly according to how fast the stick was rotated.
Finally, by varying the weight of the stones, the rate of material removal could be controlled – this phenomenon has only recently become properly understood.
It can now be seen that, as a finishing process, lapping can only produce the best possible results when all other relevant factors are taken into account and fully optimized.
With the discovery of metals, casting, forging and subsequent work operations such as sharpening (bound grit particles) became primarily important, and lapping faded into disuse. It was only the introduction of gauge blocks (Johansson), and a growing demand for better quality generally, which led to a renewal of interest in the technique of lapping.
Unfortunately however, the makers of gauge blocks kept their knowledge of lapping secret, thus preventing this modern technology from being used in other applications. But an important step forward was made when lapping was adopted as a means of improving the possibilities available in the field of optics. Nevertheless, the widely held concept of lapping as a prohibitively expensive art form remained fully anchored, and progress towards its broader application was further hindered by the poor results obtained by hand lapping methods. Hand lapping was not only inaccurate and expensive, it was also very messy, and nobody took the trouble to study the technique in depth in order to eliminate its negative aspects. It took the industrial efforts of the Second World War, with their enormous demands on quality, interchangeability and mass production, followed by those of the burgeoning automobile industry, to bring this technique of lapping into its own. Requirements for tightly toleranced dimensions, and for surface finish quantities that could be reliably achieved and standardised, finally gave the impetus for a breakthrough in the widespread adoption of industrial lapping.
Machine manufacturers also contributed to progress, and the single-plate lapping machine, incorporating conditioning rings for continuous correction of the lapping plate surface, was an important development. Applications became wider and more numerous, and lapping was soon a serious competitor for grinding, which had replaced it completely in some cases. The success of lapping was such that practical application jumped years ahead of research, as manufacturers preferred to press ahead with new machines rather than spend time asking and answering fundamental questions. No research centre was sufficiently interested to take up the subject, and practically no literature on lapping existed. Pioneering research was conducted by Prof. Dipl. Ing. K. Martin at the renowned Wuppertal Technical University, and it is due to the author of the present article that more recent work has been carried out at ETH, the Swiss Technical University in Zurich. Discoveries stemming from this work have now laid the foundations for further progress in lapping techniques. Several government-run research institutes have already started work in the field and verify the data from practical experience in most cases. Films and reference material are now available. It is worth mentioning that the successes achieved in high-tech fields such as microprocessors, compact discs, computer and aerospace engineering etc. are largely based on the possibilities offered by lapping and polishing technology.
It is hoped that this article, like its predecessors, will contribute to the further success of the lapping technique by stimulating the interest of the current experts and of the new “lapping generation. Seminars and conferences are now common and confirm that the lapping and polishing technique is now fully recognized as a modern machining method.