Fixed Abrasives Take Lapping Into Another Dimension
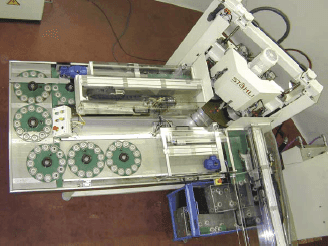
Traditionally, the grinding process known as lapping has been employed in stock removal of metal and ceramic workpieces to achieve a desired concentrically or “flatness”. The flat lapping process typically involves a slurry. Commonly, with loose aluminum oxide, silicon carbide, or other abrasive grains; flowed across a rotating lap plate in either a water-based, synthetic, or oil-based vehicle. Doing so causes an abrasive film between the plates and the workpiece. This enables stock removal from a single side or from both sides. Simultaneously, the lapping dimensions of regular or irregular shapes, surface distortion from clamping, or heat will not occur. The loose abrasives leave a dirty residue that must go through a rinsing process to clean after lapping. Controlling this loose abrasive process in most cases has to rely on the experience of machine operators.
Many companies have discovered the benefits of replacing their traditional flat-lapping operations with newer technology. This operation called flathoning refers to a process as clean lapping. Honing replaces the “black magic” associated with the intense operator involvement for consistent
finished product with today’s abrasive technology and CNC machinery.
By using bonded CBN or diamond particle in a fixed medium that replaces the loose abrasive process; flathoning achieves the same or greater precision with fixed abrasives than those accomplished through conventional flat lapping.
Carbide Insert Application
Consider a tungsten carbide insert application. Inserts might first be ground on a traditional lapping machine with special fixtures holding up to, for example, 200 units. After grinding one side, the inserts are un-fixtured, turned over, re-fixtured, and ground on the other side. Throughput averages between 200 and 300 parts an hour. Removing the typical 0.020 to 0.025 inches of stock from a tungsten carbide insert with a flat-lapping machine usually requires 2 to 3 hours because the material is so hard.
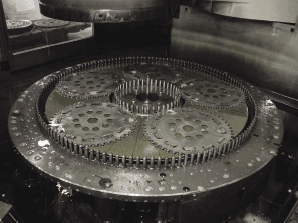
However, flathoning machines are unlike conventional fix abrasive grinders for sizing components. Clean lapping far exceeds the 0.0002- to 0.0003-inch tolerances of conventional grinders, and it takes that 0.025 inch of carbide stock off both sides simultaneously within 4 to 5 minutes. On a smaller machine, 100 to 150 inserts can finish within 7 to 8 minutes, a rate of 700 to 1,000 parts per hour. Speed is a primary reason double-side flathoning is replacing conventional grinding and flat lapping in numerous applications across many industries. One flathoning machine can often replace three to four grinders and their associated labor; and over-head or reducing it can decrease high tolerance lapping cycles to a few minutes. Stock removal rates are multiples of 10 to 20 times faster than lapping. Achieving certain tolerances are now higher than those workpieces that are undergoing a lapping process.
The Ease of Flathoning
Flathoning can hold thickness variations within 0.6 micrometers (0.000024 inch) in a single batch. With overall batch-to-batch tolerances of ±1 micrometers (0.000040 inch) on a 24-hour basis. That capability comes from using a fixed, bonded material. As opposed to a loose material, with the added ability of removing stock faster.
Traditional Grinding / Lapping Dimensions
Traditional grinding still makes sense for a high-volume single part that holds 0.0002- to 0.0003-inch tolerance and doesn’t require retooling.
Below should be in mind when considering flat honing processes:
- Parts exceed the 0.0002-inch tolerance threshold.
- Retooling a variety of jobs is necessary. Flathoning, with the proper wheels on the machine, takes less than 5 minutes to retool, compared to several hours for traditional grinding machines.
- Components have uneven surface areas between the top and bottom.
- Lapping tolerances are required, but higher throughput is necessary.
- Working nonferrous or nonmagnetic materials.
With lower abrasive costs, increased throughput, superior accuracy’s and reduced labor, the technology in flathoning can be the solution for many traditional grinding applications. Flat honing brings the completion of successful lapping into another dimension.